Construction Consulting Spotlight: Know The Best Practices for Flat Roof Replacement, Upgrade, Maintenance
There are many options and solutions to choose from when it comes to commercial roofing projects. Beacon Consulting Group (along with our sister company, Beacon Merchant Construction), has extensive experience managing the replacement, repair, and upgrade of flat roofing systems. Knowing the ins and outs of roofing system specification, as well as the ability to properly manage the installation (and/or renovation) process is critical to ensuring that the completed project will perform according to manufacturer’s specifications and for achieving the desired service life.
A plethora of products and options now exist for flat (or “low-slope”) roofing systems. The most common categories of roofing systems now include:
- Asphaltic Roofing Systems: Including Built-Up Roofing (BUR), Modified Bitumen Systems (MBS) and Composite Systems
- Liquid-Applied Roofing Solutions
- Membrane-based solutions (made of PVC, EDPM rubber or other materials)
There are other types of systems for flat roofs, including “green / vegatative roofs” (where ground cover or gardens cover a rooftop), metal roofing, and various spray-on / roof-sealing solutions, such as spray polyurethane foam-based (SPF), and rubberized spray sealants. However, this article focuses mainly on BUR systems.
Which system to use for a particular project depends on many factors, including:
- Usage factors (such as whether there will be decks or foot traffic on the roof, location, and visibility/aesthetic requirements)
- Pre-existing roofing and physical roof conditions
- Weather conditions
- Insulation requirements
- Desired service life
- Local building codes
- Budget constraints
Roofing system manufacturer warranties range from anywhere from 10-30+ years, depending on the system applied. However, proper installation is critical to ensuring that a roof will have many years of leak-free service. Following best practices (and manufacturer recommendations) for installation is also necessary to ensure that a manufacturer will honor its warranty.
Built-up roof (BUR) systems have traditionally been the least expensive of the main types of flat roofing systems, but costs can vary depending on specific products / applications. BUR systems typically consist of multiple plies of waterproof material, alternated with hot asphalt (and surfaced with stone, such as river stone, or other aggregate). BUR is installed over wood, concrete, steel, or foam insulation and is “built up” in stages like a layer cake.
A base sheet (typically asphalt-coated or fiberglass material) is applied first. Many roofing contractors will next install all required flashing (to ensure a seal around vent pipes, scuppers, and other structural features or around mechanical / HVAC equipment structures found on the roof). Properly installing flashing using the correct materials, procedures and sealants/cements is critically important. According to roofing experts and manufacturers, 90% (or more) of leaks in BUR roofing systems occur at locations where flashing details are located, because those locations are where weaknesses/openings are most likely to occur.
It is normally necessary to heat the “sealing layers” (of hot asphalt / bituminous tar) used between layers of ply in BUR systems. Its common to have at least three layers of “felt” ply that is rolled out and “fused / sealed” together using layers of hot asphalt. Hop mop or “torch down” (open-flame heating) methods are often used during the installation of built-up roofing systems, when rolling out or sealing between layers to ensure a secure, waterproof seal and proper adhesion of the layers of felt ply. When using the torch-down heating method (or hot mopping), site safety and using highly experienced installers is especially important. Most roofing system manufacturers provide training and certification programs to ensure that contractors understand best practices for each step in the roof installation process (for safety and performance).
The top layer of BUR systems is normally covered with aggregate (crushed stone or gravel) to protect the roofing materials from UV rays. The aggregate also improves the fire resistance of the roofing system. Similarly, roofing cement used to seal flashing should also be protected using a special UV-resistant paint. For hot climates, it can be economical to install a “cool roof” system, where the aggregate used is light colored (such as crushed dolomite/marble, or light-colored granite, quartzite, or limestone). Light-colored aggregate reflect sunlight and heat away from a building, thereby reducing roof temperatures by 50 degrees (F) or more during very hot / sunny days. This can result in greatly reduced building cooling costs and longer life for the roofing system.
Some of the major issues / problems that can occur with flat roof systems are noted below. These issues can generally be avoided by proper specification, installation, and maintenance. Routine maintenance and inspection can help to identify problems early, before the issues noted below lead to more serious (and sometimes catastrophic) roof issues.
Some common problems that can occur related to flat roofs include:
- Leaks / moisture intrusion – Particularly around improperly installed or poorly sealed flashing (and other irregular features / protrusions found on roofs where there is higher potential for gaps and cracks compared to uniform/flat section of the roof)
- Ponding of water – Roofs must be designed to have adequate drainage systems (with gradual sloping in appropriate locations). HVAC systems without proper condensate drains can be one source of water pooling that can lead to issue
- Unexpected foot traffic or new structures being built leading to damage (or punctures) to existing roofing surfaces
- Improper surface preparation (leading to poor adhesion of layers or voids that can create “weak spots” where leaks or punctures can more easily occur)
- Blisters, delamination, material shrinkage, and splitting can occur over time – particularly if asphalt sealing was not heated adequately during the sealing process (prevent a uniform and continuous seal between layers in BUR systems)
- Improperly sealed / coated areas where parapet walls are located
Beacon’s team includes several project managers with extensive experience in the evaluation of roofing systems and the management of flat-roof installation and renovation projects. Our team can specify, source and manage valuable inspection services for evaluating existing roof systems. These include:
- Visual inspections and reports (e.g. identifying problem areas, such a damaged flashing, pooling, blistering, and other vulnerabilities).
- Infrared (IR) Thermographic Roof Moisture Analysis – IR technology can be used to detect areas of moisture intrusion within a multi-layer roof system.
- Managing more in-depth technical inspections (electronic leak detection) for early detection of roof leaks.
Contact Beacon Consulting Group, Inc. for any construction-defects-related assignments, construction consulting/management projects, or surety consulting services.
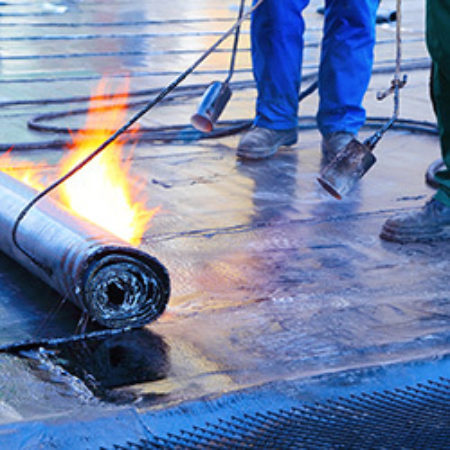