Investigating & Resolving Building Roof Issues With The Help of Infrared (IR) Inspection Technology
Beacon Consulting Group has consulted on many large roof construction, replacement and inspection projects in recent years, both as the Construction Consultant for leading Sureties and for insurance claims / construction defects investigations. Infrared roof (IR) inspections and IR roof survey reports are valuable tools for investigating roofing issues.
Thermal imaging inspections (using IR thermography cameras) can be a reliable and efficient way to find (and map) water leaks and hidden moisture areas in roofing systems. Water intrusion is a pretty common problem on flat, multi-layer roofs used on most large commercial, industrial and residential buildings. The root cause of moisture intrusion can be the result of a variety of different possible issues: Improper installation or maintenance of the roof system, poor seal around structures and equipment found on the roof, normal aging of the roof, damage from weather events, accidental damage during construction or vandalism.
Thermal cameras and inspection reports help pinpoint and document where moisture has penetrated a roof by providing a visible, color-coded thermal image which reveals temperature differences between dry places and moist areas. IR inspections are typically more effective after sunset (or later afternoon), because the infrared camera's images will more clearly reveal temperature differences between dry areas and moist areas (wet sections retain heat longer and release heat slowly into the evening hours). Heat being released by moist areas of the roof can typically be identified very quickly be a skilled IR inspection technician.
Some examples of how IR roof inspections were applied to assist a Surety in their investigation on projects where Beacon was providing construction consulting services:
- Surety Consulting Project / Data Center Roofing Sub-Contractor Default: When inconclusive scanning was performed by both the Roofing Contractor & General Contractor at a large data center in the Southeast, IR Thermography was used to identify specific areas where moisture was intruding through the facility's large, built-up roof which was under construction. An IR inspection survey and report helped to confirm that only select areas of the roof needed repair (helping to avoid expensive replacement of large roofing sections as requested by the General Contractor and potential penal sum loss to the Surety).
- Surety Consulting Project / NYC Public Housing Project: Following default, an IR Thermography inspection was used to confirm that a previously installed roofing system on a public housing project (residential high-rise tower) was free of water intrusion following a lengthy termination process by the Owner. The IR inspection and report was a necessary step to provide the project owner and roofing manufacturer with verifiable proof that the work was completed successfully in order to obtain contractually required Roofing warranties.
Depending on the workscope and goals for any given roof inspection, a good IR inspection firm will provide:
- A report which includes a description of their findings (such as how many areas appear to have moisture / water intrusion)
- An accurate map (such as a CAD file) delineating areas where moisture was found
- The report will also include IR image captures for the scanned areas, with detailed images for any areas showing possible moisture intrusion.
- A description of findings from any “core samples” taken from areas of the roof which appeared to have water trapped under the roof surface based on the IR Inspection. Core samples are used to definitively verify whether moisture is present or not.
- Marking the roof (with spray paint) to identify areas of the roof which may have moisture intrusion
Among the many uses for IR roof inspections and IR surveys are:
- Identifying if a roof is leaking by revealing areas where moisture is building up underneath roof surfaces
- Determining if a full roof replacement is needed or only selective repairs
- Helping to pinpoint water entry points and interior paths followed by water
- Validating that a new, repaired or replacement roof is leak free
- Helping to determine where damaged, wet or missing insulation is located
- Helping to rule out roof issues when looking for sources of interior water damage
- Roof warranty investigations
When selecting an IR contractor, it’s important to verify that they have experience providing inspections and reports for similar roof configurations and problems. Also important is to have a clear scope of work (in terms of deliverables) and understanding of what specific areas will be inspected, what the company’s inspection report will include, and what the vantage point will be for IR inspections. For “before and after” scans (to verify that areas that have been repaired to eliminate moisture intrusion), it’s important to capture IR images from the same vantage point(s), at the same time of day (or evening) and under similar weather conditions.
Advances & New Technologies. A number of IR inspection companies are now offering aerial inspections where an IR camera is mounted on a remotely operated drone. Benefits of drone-based IR inspections can include:
- Ability to more quickly scan and map very large areas with minimal manpower
- No need to access a building’s roof (which can be safer, particularly for evening inspections)
- Can be less costly option for very large roof inspections
A factor which is making IR roof inspection more affordable in recent years is more competition in the IR inspection and IR camera market. Competition has resulted in the development of lower-cost, high-accuracy IR cameras in recent years.
Nuclear Moisture Inspection Devices. In addition to using infrared (IR) inspection cameras (and visual inspection), roof inspection specialists sometimes use nuclear-based moisture density detectors to accurately check points on a roof for moisture intrusion. Unlike IR scanners, nuclear-based inspection devices are placed directly on the roof surface at specific areas to be tested. This option is often used when a roof has characteristics that inhibit IR inspection, such as highly reflective roofing surfaces and/or roofs covered with gravel material (ballasted roofs). With these types of moisture density gauges, a shielded nuclear source within the device emits neutrons downward into the roof. Detectors in the device measure changes in the speed of those neutrons as the collide with neutrons of hydrogen present in moist areas.
Nuclear moisture detection can be a very accurate method to map the degree of moisture intrusion in specific areas of a roof. A nuclear roof moisture survey is often conducted on a grid pattern across the area to be inspected (using uniform grids, such as 5’x5’, 10’x10’ or 20’x20’). On ballasted roofs, gravel must be temporarily pushed aside at the inspection sites to position the gauge directly on the roof surface.
Beacon’s team is experienced with helping to develop roof inspection workscopes, selecting qualified inspection companies, monitoring inspection work as it progresses, and interpreting/summarizing inspection reports for clients.
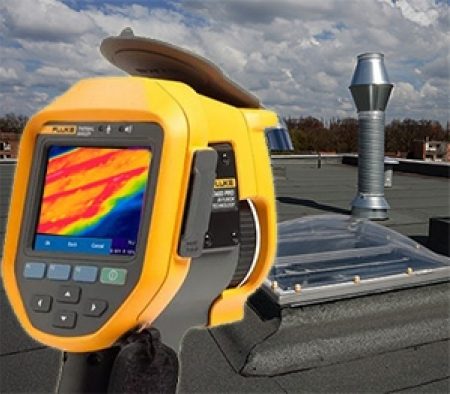